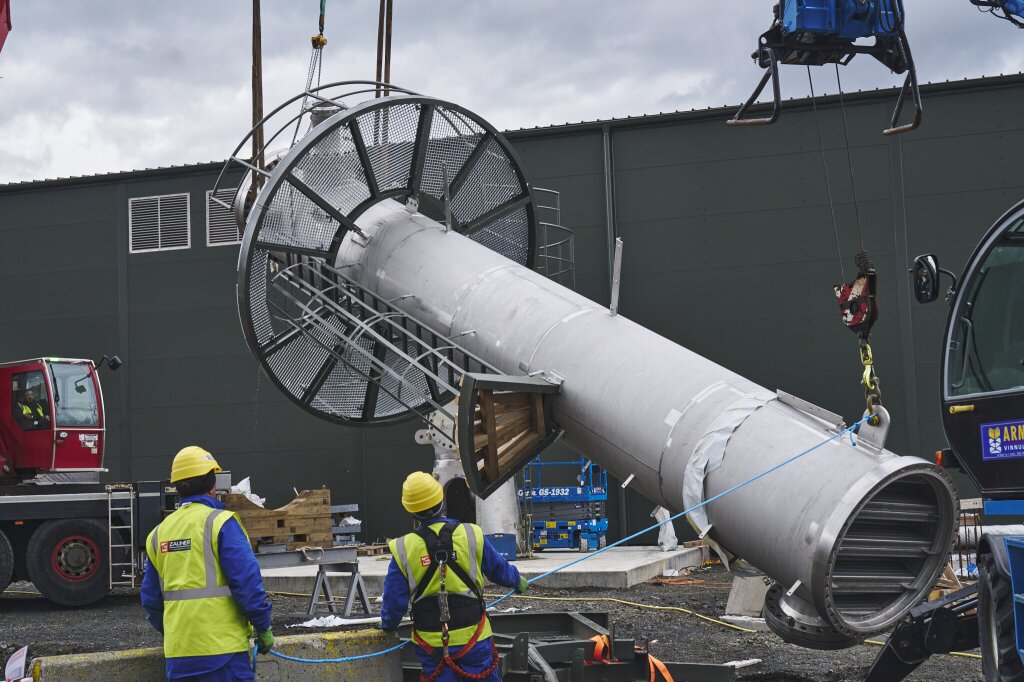
Mammoth: innovating the DAC+S process with a CO₂ absorption tower
Mammoth, Climeworks' DAC+S plant currently under construction, is making steady progress in Iceland with a CO₂ absorption tower developed by Carbfix.
How the overall equipment effectiveness (OEE) used across industries
applies to capturing then reaching net removal of CO₂
Offering an effective way of permanently removing carbon dioxide, direct air capture (DAC) technology is gaining traction globally. On the voluntary carbon market, the private sector’s demand for carbon dioxide removal (CDR) via DAC has surged, and political support is increasing as well – demonstrated by laws such as the Infrastructure Investment and Jobs Act and Inflation Reduction Act.
One of the critical strengths of DAC is its verifiability: the CO₂ can be precisely measured and reported along the process. With this article, we want to explain the carbon removal production steps of DAC and offer a new tool for other CDR industry actors and technological approaches to drive the discussion forward with a common understanding of key terms, and a robust approach to numbers and delivery expectations when interacting with all stakeholders including the general public.
When a DAC plant captures a CO₂ molecule, that molecule goes through several steps before it is permanently stored and the removal is produced.
Here’s an overview of all the steps of a DAC plant’s CDR production and the factors influencing it:
The CDR production process starts with the nameplate CO₂ capture capacity, which is the nominal amount of CO₂ that a DAC plant can capture based on average site conditions, operating with 100% availability for a full year (= operating at maximum capacity without interruption for a full year). Such a nameplate capacity is a standard way to classify process plants.
The actual net CDR produced is lower than the nameplate capture capacity. The main factors responsible for this difference are the overall equipment effectiveness (OEE), which includes the availability of the plant, the performance, and recovery of the process, as well as grey emissions.
For first-of-a-kind (FOAK) process plants, such as Climeworks’ Orca, it is expected that the produced net output (in this case net CDR) is lower than its design values. The purpose of such FOAKs is to gain field experience and prove the full-chain production process works under real-life conditions, which involves testing and finetuning.
Read about each factor and how it influences CDR production in more detail below:
The available CO₂ capture capacity is the effective maximum amount of CO₂ a DAC plant can capture during a year of regular operation. In practice, plant availability of process plants is lower than 100%, for example, due to stoppages for planned and unplanned maintenance or power supply interruptions. On average, the available CO₂ capture capacity is typically 5-15% lower than the nameplate capacity.
CO₂ captured is the actual amount of CO₂ a DAC plant captures during its operation. This may positively or negatively deviate from the average available capture capacity due to various factors associated with the performance of the capture process. On average, the amount of captured CO₂ can be up to 20% higher or lower than the available capture capacity, fluctuating over time depending on external factors such as weather conditions as well as the degradation of the sorbent material.
The CO₂ stored is the amount of CO₂ that can be recovered and stored after the capture process: after capturing, the CO₂ is conditioned before delivery to storage. Conditioning can include purification or condensation of the gas. CO₂ losses can occur during the conditioning phase. On average, the amount of CO₂ delivered for storage is typically 1-10% lower than the amount of captured CO₂.
Annual (net) CDR production capacity: the net CDR capacity is lower than the amount of CO₂ that has been stored because the grey emissions of the direct air capture & storage (DAC+S) plant have to be accounted for: they are deducted from the stored CO₂, i.e. the DAC+S plant removes its own footprint, which is therefore excluded from the net CDR capacity. The main sources of such grey emissions include project-related sources (e.g. concrete, steel), sorbent-related sources (e.g. sorbent production for regular sorbent exchanges), and energy consumption (even in the case of clean energy, e.g. due to the manufacturing of solar panels). On average, the annual CDR production capacity can be around 10-15% lower than the amount of stored CO₂ due to the grey emissions, but exact numbers depend on the exact plant configuration and energy supply. Climeworks sells only the final net CDR to its customers.
As of 2022, Climeworks provides third-party verified CDR services performed at its Orca plant in Iceland to its customers, meaning that every step of the CDR production process is precisely measured, and verified by an independent 3rd party – from CO₂ captured to net CDR capacity.
When DAC technology is combined with storage to provide permanent carbon removals, the annual (net) CDR production capacity is the right metric to look at when talking about a DAC plant, as it incorporates all CO₂ losses along the process and accounts for plant availability and grey emissions.
Following the logic of this CDR production waterfall, Orca’s annual CDR production capacity is up to 3,000 tons while its nameplate capacity is up to 4,000 tons of CO₂ per year. As a FOAK plant, Orca’s purpose was to gain field experience and prove the full-chain process of DAC+S works under real-life conditions while providing high-quality CDR to Climeworks’ customers already today. In this context, Orca’s maximum annual CDR capacity has not been achieved yet as plant availability has been significantly lower due to several reasons, such as tests, improvements of the design, maintenance, harsh weather conditions or electricity interruptions. Read more about it in this recent coverage on the topic.
As Climeworks scales up, it will deploy new technology generations in ever-larger plants that will all follow the CDR production waterfall and offer our customers CDR services that are permanent, additional and verifiable.
Mammoth, Climeworks' DAC+S plant currently under construction, is making steady progress in Iceland with a CO₂ absorption tower developed by Carbfix.
Enabling third-party certified carbon removal via direct air capture
Our approach to permanent carbon removal via DAC technology
High-quality carbon removal for your climate strategy.
No cookies = No worries: We don’t use 3rd party cookies and only use the cookies we strictly need to keep our website functioning. Our website usage data is 100% cookie-less, anonymized, and under our full control. For more information, please check out our privacy notice.