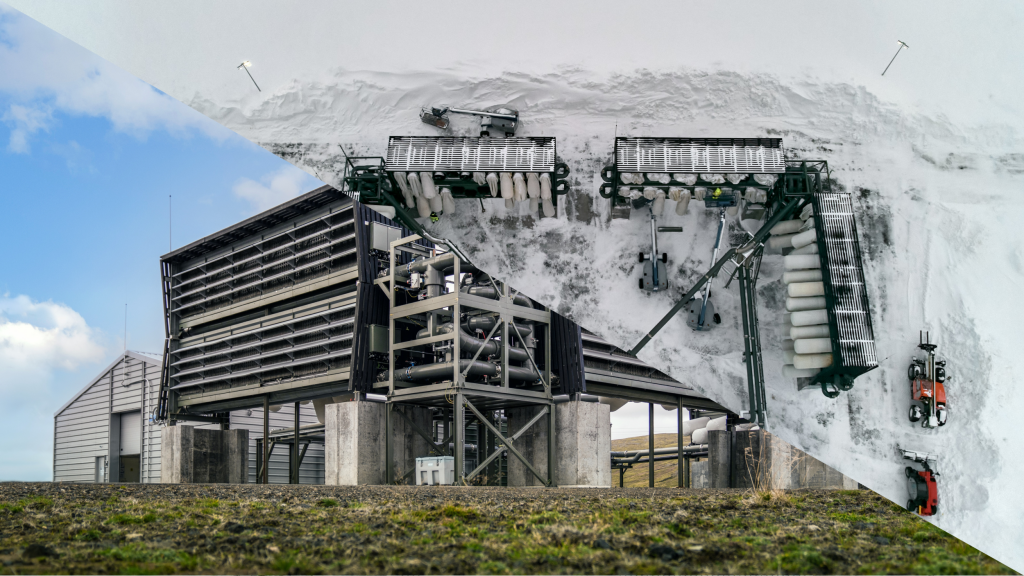
Key take-aways
Climeworks is leading the field of direct air capture (DAC) for many years due to a combination of two elements that are today still exclusive in our field: we unite cutting-edge research and development (R&D) with thorough technology deployment in the field.
Our 150+ full-time employees in the science and R&D team work on the latest DAC technology and materials, building on fifteen years of development history.
Climeworks’ field deployment is driven by continuous on-the-ground experience, achieved through the construction of multiple real-world plants in rapid sequences. Through fast iterations and rigorous tests, Climeworks ascertains the most effective methods for success, ensuring operational excellence in our scale-up journey.
Climeworks’ DAC field experience based on commercially operating plants dates back to 2017 – with the world’s first commercial plant, located in Switzerland. Our journey of high-quality carbon removal via DAC was kicked off with our first demonstration in Iceland in 2017, which led to our Orca facility in Iceland in 2021, the world’s first commercial direct air capture and storage (DAC+S) plant.
Orca has been instrumental to Climeworks’ steep learning curve, proving the full DAC+S process under real-life conditions and providing invaluable insights on its performance and operational challenges.
This article provides an opportunity to look behind the scenes of Climeworks’ field deployment journey.
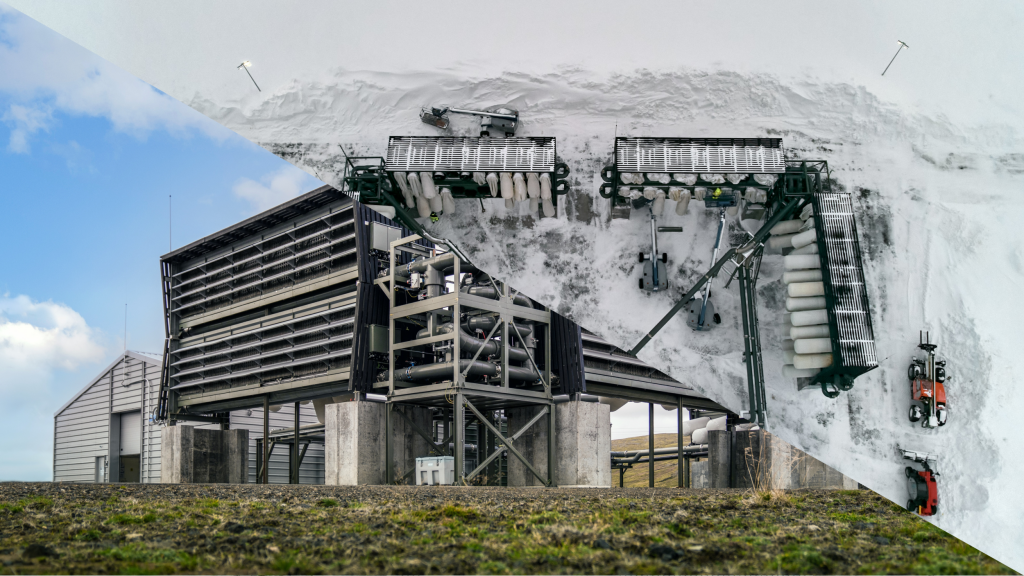
Deploying a new technology in the field differs drastically from developing it in the lab. Evolving from research in the lab to field deployment is often accomplished through building and operating a first-of-a-kind facility. Such first-of-a-kinds prove that an idea or process that previously existed only in theory or on a small scale works in the field and can be scaled up to meet commercial demand.
This is exactly what Climeworks’ Orca plant was developed and built for: proving the full-chain DAC+S process in the field and providing a supply of high-quality carbon removals to meet the ever-increasing commercial demand.
Starting deployment in the field is a tough journey. Many unknowns are encountered on the way and lots of troubleshooting is involved. Having operated Orca for more than two years now, Climeworks can look back to many learnings, which are instrumental to the company’s next scale-up steps.
Where we are today
Is Climeworks where we wanted and expected to be?
Yes, in many ways, our progress exceeds even our own expectations. But we have higher ambitions and are on track to make our gigaton removal by 2050 happen.
Our deployment journey began in 2017, when Climeworks commissioned its very first commercial DAC plant in Hinwil, a small town close to Zurich, Switzerland. When we show this facility to visitors, we often refer to it as the birthplace of modern direct air capture: it is the world’s very first commercial DAC plant and enabled Climeworks to scale to a size that was never achieved before and, more importantly, evolve from the lab to real-world deployment. Since then, we have commissioned two additional commercial plants, a second one in Hinwil and Orca in Iceland, and are completing our fourth and, to date, largest plant Mammoth in Iceland. Our field experience accumulates over 120,000 operational hours across different climatic conditions, making us the world’s by far most deployed carbon removal company with direct air capture at the core.
But we are not stopping here, our deployment journey has only just begun. Our international expansion points towards future growth on a global level. Starting from global headquarters in Zurich, Switzerland, Climeworks grew to more than 500 employees across Switzerland, the United States and its offices and operations in Germany and Iceland. We are actively developing projects in various geographies across the globe, including the U.S., Kenya, Canada, Norway, and the Middle East.
While speed is critical, we are determined to keep scaling responsibly. Offering the highest-quality carbon removal service to our customers takes absolute priority, which is why we advocated for and invested in robust monitoring, reporting and verification (MRV) standards early on. The carbon removals we perform at Orca are third-party verified by DNV and we are in the process of achieving third-party certification under the Puro Standard as the first direct air capture company. Pioneering DAC+S assessments and advancing MRV efforts to this level is only possible thanks to our multi-year deployment expertise in the field. Climeworks’ Orca plant has long been the world’s only active commercial carbon removal project based on direct air capture with permanent geological storage. The resulting field experience informed the formulation of certification methodologies and enabled verification in the first place. It set the precedent for Climeworks’ future plants and the direct air capture industry more broadly.
Yet, in some respects, we hoped to be even faster.
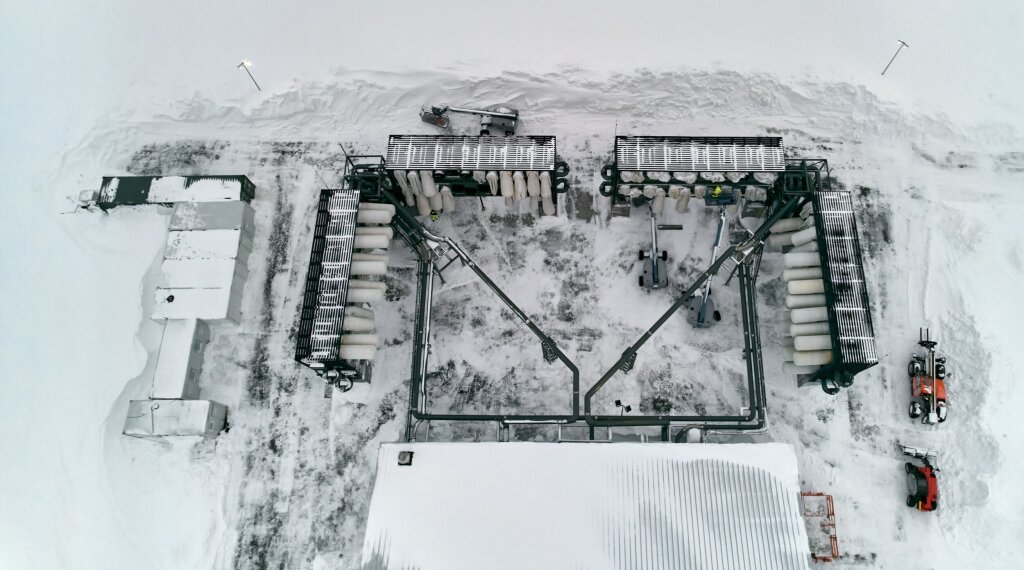
Orca shows the reality of operating a first-of-a-kind facility in the field and how this reality can differ from design values in various directions. The plant is designed for a nameplate capture capacity of up to 4,000 tons of CO₂ per year, which translates into a design net carbon removal capacity of approximately 3,000 tons per year, based on our carbon removal waterfall production model. After having operated Orca for more than two years, we can show three main kinds of deviations from these design values.
First, the filter material (sorbent) that was used for the first fill of Orca was an early version within our sorbent material portfolio (note that the sorbent material currently contained in the Orca plant still corresponds to this early sorbent, representing the state of the art of Climeworks’ DAC sorbents of about 2019).
On the one hand, its performance as measured by CO₂ uptake over a given timeframe was around 10-20% below design specification at production specification freeze (design specification refers to the end point of the design phase at which a technical product description is handed over to production; production specification refers to the set of requirements that the entire design of the product is based on).
On the other hand, quality fluctuations of up to 20% during the sorbent production process led to a lower actual material performance of certain production batches, which we decided not to correct to maintain Orca’s operation schedule. Those quality fluctuations have been rectified in the meantime and this material type can be produced with less than 5% quality fluctuations between batches.
All this results in a lower overall nameplate capture capacity of 3,000-3,100 tons of CO₂ per year, corresponding to 2,400-2,500 tons of maximum achievable annual carbon removal capacity.
It should be noted that today’s materials benefit from more than five years of subsequent development and optimization compared to the first-fill Orca material. Climeworks’ R&D focuses strongly on the development of cutting-edge sorbent technology, with a team of 30+ chemists and material scientists dedicated solely to this challenge. For example, the latest sorbent material formulations result in about 20% higher capture capacity compared to Orca’s first fill.
Second, the design availability (uptime) of the plant has not yet been reached on a yearly average due to operational interruptions that are inherent in deploying a first-of-a-kind plant. This means Orca has not run at its maximum possible capacity, yet. Challenges include extreme weather conditions in Iceland, which led to equipment downtime due to icing, and exposure to contaminants in geothermal water, which accelerated equipment wear.
Another challenge relates to the supply chain: to meet our accelerated deployment schedule, choices were made to proceed with components that had a lower service life, for example, carbon steel instead of stainless steel, for which planned downtime to upgrade was needed. It is important to prioritize speed to market when looking to develop new technology to allow learnings to be harvested as quickly as possible. Such choices also provided data to assess service life and maintenance intervals, allowing us to establish the true lifetime limits of these components.
As a deployed and operational plant, Orca moreover offers an important opportunity to conduct rigorous testing in field conditions, relevant to our future plants. Such tests led to several interruptions of Orca’s operations but provided crucial insights for future plant designs. For example, prototypes of improved versions of our collector container technology were translated into upgrades implemented at Mammoths’ collector containers, such as improved chamber sealing concepts and coating specifications. Overall, operations at Orca yield over 180 million operational data points every day, which provide an invaluable lever to further optimize process performance.
And third, Orca operations in the plant’s early days had significant recovery losses of up to 30% of the captured CO₂. The CO₂ had to be vented off into the atmosphere, as it did not meet the purity standard for the post-capture liquefaction process at Orca. As a mitigation, we installed additional equipment that allows us to decrease these losses by around 90%. Based on these learnings from Orca, the Mammoth plant was simplified and uses an absorption column in place of a liquefaction process that significantly lowers the dependence on CO₂ purity, therefore addressing the root cause of recovery losses.
The filter material, recovery rates and interruptions caused by operational challenges and testing, also influence Orca’s life cycle emissions. Life cycle emissions are a facility’s grey emissions over its entire lifetime, from construction to decommissioning including the grey emissions of consumables and energy used by the plant. In 2021, an independent lifecycle assessment found that the Climeworks technology at its development stage at that time has the potential of achieving less than 10% of life cycle emissions, with further optimization potential for future technology generations. In other words, over its whole lifespan (including construction, operations and recycling), a plant would re-emit less than 10% of the carbon dioxide it captures. Orca has realized 20-25% of life cycle emissions in 2023 because the energy needed to produce a ton of carbon removal was higher due to the plant’s below-design production levels. In 2024, we have seen the energy and hence grey emissions reduce and meet our design expectations with improved operational efficiency and throughput.
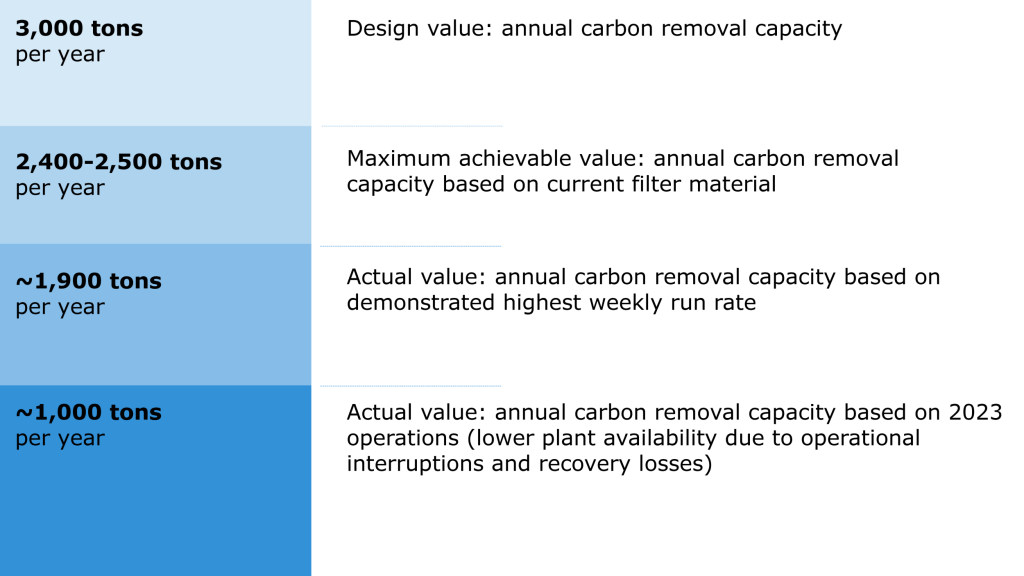
As a first-of-a-kind plant, Orca’s main value is to provide us with operational experience under real-life conditions – which Orca is constantly delivering. The operational hours we gained in the field provided us with numerous learnings that lab experiments could never have.
What we learned on the way
Operating Orca proves that only by deploying direct air capture in the field under real-life conditions can the industry make real and tangible progress on the technology. Climeworks has a better understanding of direct air capture than any other DAC company thanks to the progress and learnings it gained from operations. And we are more convinced than ever that DAC will play a crucial part in climate change mitigation. The following learnings explain why.
The obstacles we have come across are all solvable
While DAC technology is new, the operational challenges encountered at Orca are not. Ramping production capacity to maximum throughput is a challenge for any manufacturing facility and usually takes several years with any hardware equipment. This is not unique to direct air capture, but observed for any hardware technology company doing early field deployments. Direct air capture “manufactures” negative CO₂ emissions, Apple manufactures phones and laptops, Tesla manufactures vehicles – we are all confronted by the same obstacles when ramping up first production. Orca’s operational performance has increased consistently since start of production. In 2023, each quarter performed better than the one in 2022 (see figure).
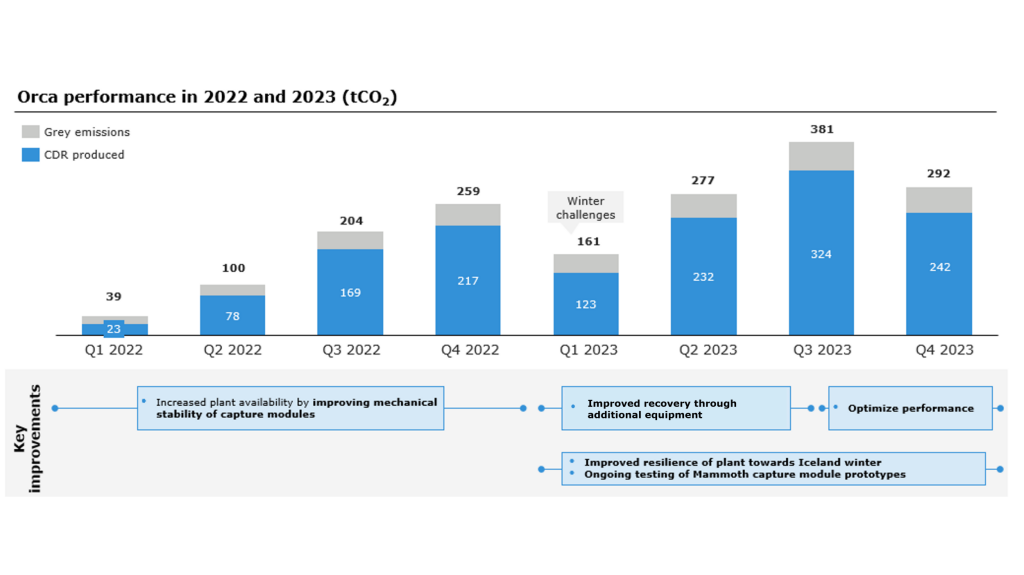
The improvements resulted in the best consecutive seven days of production in the first quarter of 2024, where Orca demonstrated a carbon removal production rate of 1,900 tons (annualized), representing roughly 80% of the maximum achievable carbon removal capacity (2,400-2,500 tons per year). This output was achieved with a sorbent that was already in use for two years, therefore operating with degraded performance. It implies that today, we can achieve a carbon removal production rate of over 2,000 tons per year over the average lifetime of the sorbent used.
The continuously improving outputs are expected to translate into a higher annual carbon removal production for 2024 and beyond as the plant accumulates operating hours in the now-improved architecture. The learnings and improvements made to Orca have been implemented directly into Mammoth including improved mechanical robustness of the collector containers, and a more efficient CO₂ conditioning process to reduce recovery losses.
Quality and transparency are key
A core principle of Climeworks’ deployment pathway has always been a strong focus on quality, measurability, and verifiability. No matter the operational challenges or speed of scale, we prioritize the quality of our carbon removal services, making sure our carbon removal solution is permanent and additional. Climeworks is the first DAC company that has delivered third-party verified carbon removal to its customers. The current market shift away from traditional offsets to high-quality removals and higher industry standards proves that this was the right thing to focus on and we will continue pushing for more quality and standardization in the industry.
Similarly, the industry can only scale fast enough if the first movers share their learnings – which is what we aim to do with this article and with numerous other external touchpoints, like our annual Carbon Removal Summit. As part of our efforts to third-party certify our carbon removal, we will moreover issue our removal credits transparently on a public registry.
Operational excellence needs a world-class team to maximize CDR production
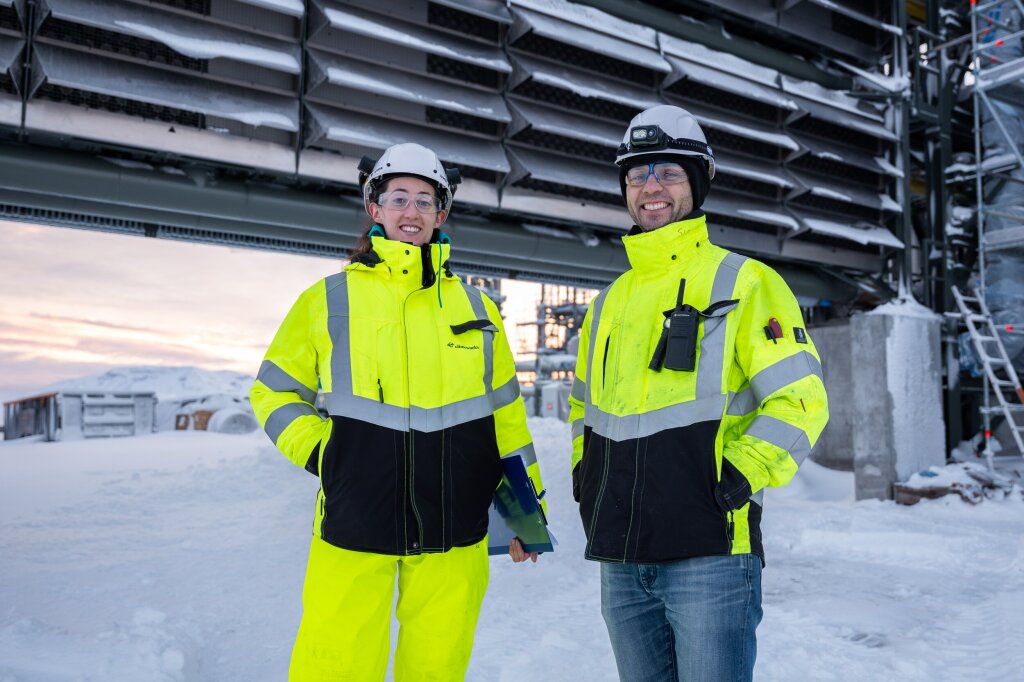
While designing, building and operating a DAC plant the size of Orca has never been done before, the fundamental principles of production remain the same as in other industries. We have a great combination of seasoned industry professionals, and intelligent hard-working minds that have implemented best practices from operating manufacturing and industrial facilities. We have established key accountabilities across production, maintenance and engineering, with an operating rhythm that allows for fast, cross-functional problem solving and continuous improvement. We are monitoring key performance indicators (KPIs) on a daily basis and our team understands how these KPIs need to be optimized to achieve maximum CDR output every day.
Global structured supply chains need to be developed
For direct air capture to scale, we need to develop a specialized, structured global supply chain. Shorter lead times and larger available quantities of parts and materials used to build DAC plants will contribute to growing the DAC industry faster and enable economies of scale, while avoiding failure of equipment that was not developed to serve the environmental conditions occurring at DAC plants. To this end, Climeworks has significantly diversified its supplier network in the past two years and will continue to do so.
Where we’re headed
To protect our planet and ensure a livable future for generations to come, the global temperature increase should be limited to 1.5°C above pre-industrial levels. This goal was agreed to by almost all governments as part of the 2015 Paris Agreement. Achieving it requires both unprecedented emission reductions and carbon removal to counterbalance residual emissions to reach net zero CO₂ emissions by mid-century. Climate science estimates that by 2100, 100-1,000 gigatons of CO₂ need to be actively removed from the atmosphere.
To meaningfully contribute to this, Climeworks’ North Star is reaching gigaton carbon removal capacity by 2050, and the experience we gained in the field has made us even more confident that we will achieve this. The steps we have taken so far are in line with our ambition of scaling by one order of magnitude every three to four years. Commissioned in 2017, Capricorn in Switzerland moved us to hundreds of tons of capacity, Orca to thousands in 2021, and Mammoth will move us to tens of thousands in 2024/2025. Our next projects in the U.S. will continue to move us to hundreds of thousands in a first phase, and then to a megaton by 2030 – the next big milestone before gigaton by 2050.
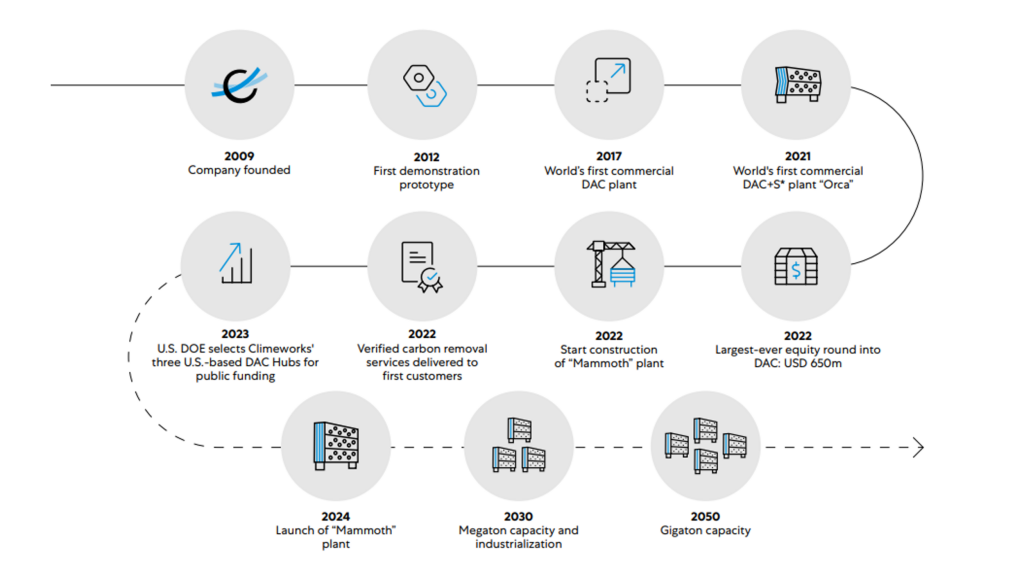
How will we accomplish this journey? Based on four pillars:
Technology leadership: in parallel to deploying on-the-ground plants in rapid sequences, we will continue to lead in DAC innovation by developing cutting-edge technology and materials in our R&D and science teams.
Quality: We will continue prioritizing the quality of our carbon removal services, making sure that each ton of CO₂ we remove for customers is durably removed, verifiable and additional. With this we hope to lead the whole industry toward more standardization and transparency.
Scale: Our focus is on drastically scaling our direct air capture infrastructure in the coming years based on an integrated model. We own the entire value chain of direct air capture, including R&D, project development, construction, operations and our carbon market platform – competency across the full scope makes us the clear market leader.
Global roll-out: We are pushing boundaries, developing DAC projects across the world, both in developed countries as well as the Global South. We believe the emerging DAC industry can benefit everyone and will focus on projects with the greatest impact.
We are determined to continue leading across all four pillars and are convinced that DAC will have a scalable impact on tackling climate change because of the operational excellence we developed over the years – backed by a highly skilled team that can take on any challenge that we might face in the future.
Lead the race toward net zero
High-quality carbon removal for your climate strategy.